A MEANS OF REDUCING SPONTANEOUS BREAKAGE
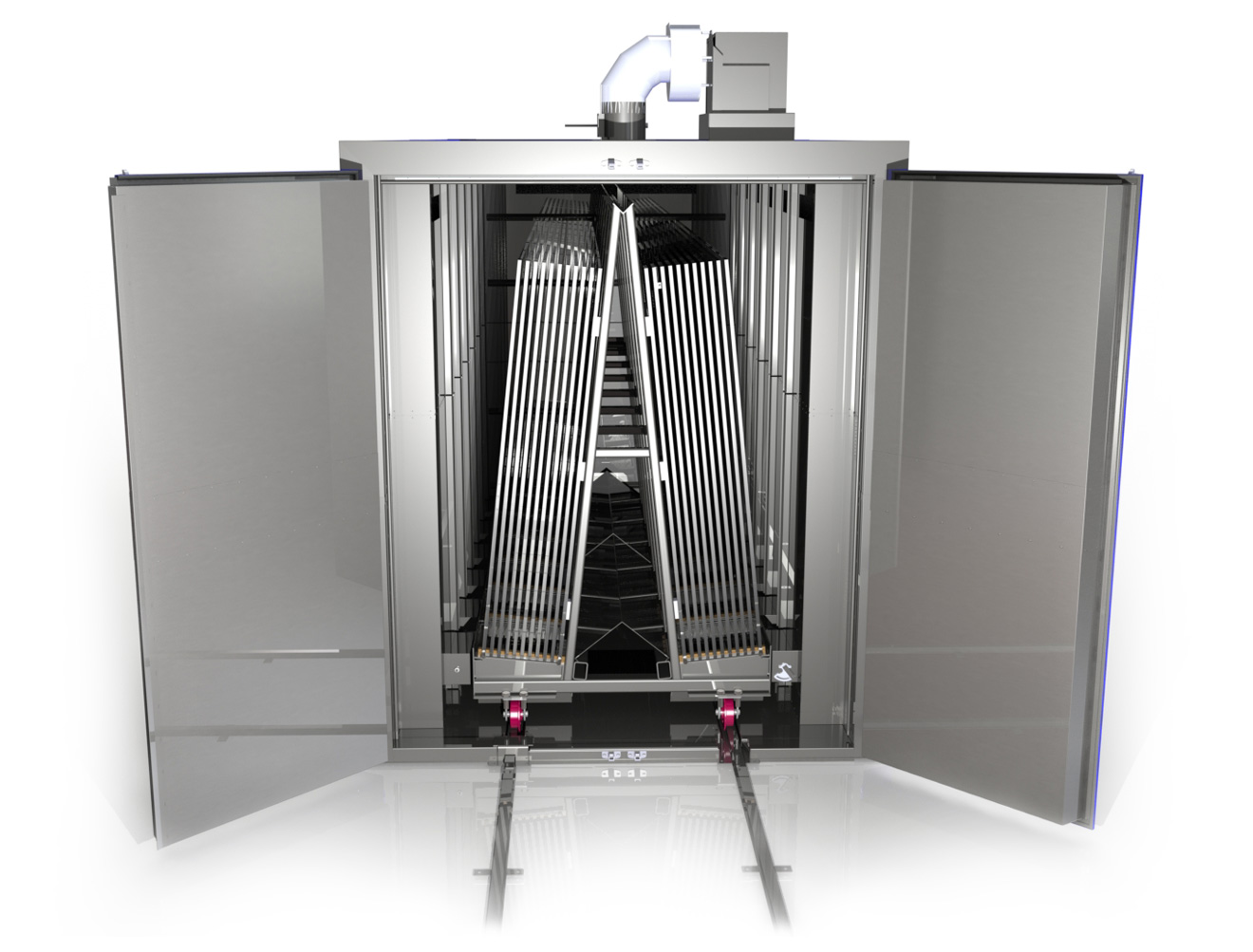
In architectural glazing applications, the use of heat-treated glass considerably reduces the breakage potential due to stress-induced by temperature change and strain from wind and snow loads. In most cases, safety glazing is required by applicable building codes and fully tempered or laminated heat-strengthened glass is often specified.
TEMPERED GLASS CHARACTERISTICS
The most commonly used type of safety glass is tempered glass, which is made by heating pre-sized glass panels to about 650°C (1200°F), then rapidly cooling them through quench. The result of using a fast quench is a glass panel with surfaces and edges in compression, and the center of the glass in tension.
Tempered glass is four to five times stronger than conventional glass, and the tempering process dramatically changes the break characteristics of the glass. When tempered glass is broken, it shatters into tiny cube-shaped pieces rather than shards. This drastically reduces the potential for injury caused by sharp edges. Despite the high strength and desirable breakage characteristics, tempered glass is uniquely vulnerable to a catastrophic failure mode that is often referred to as spontaneous breakage.
FLOAT GLASS CHARACTERISTICS
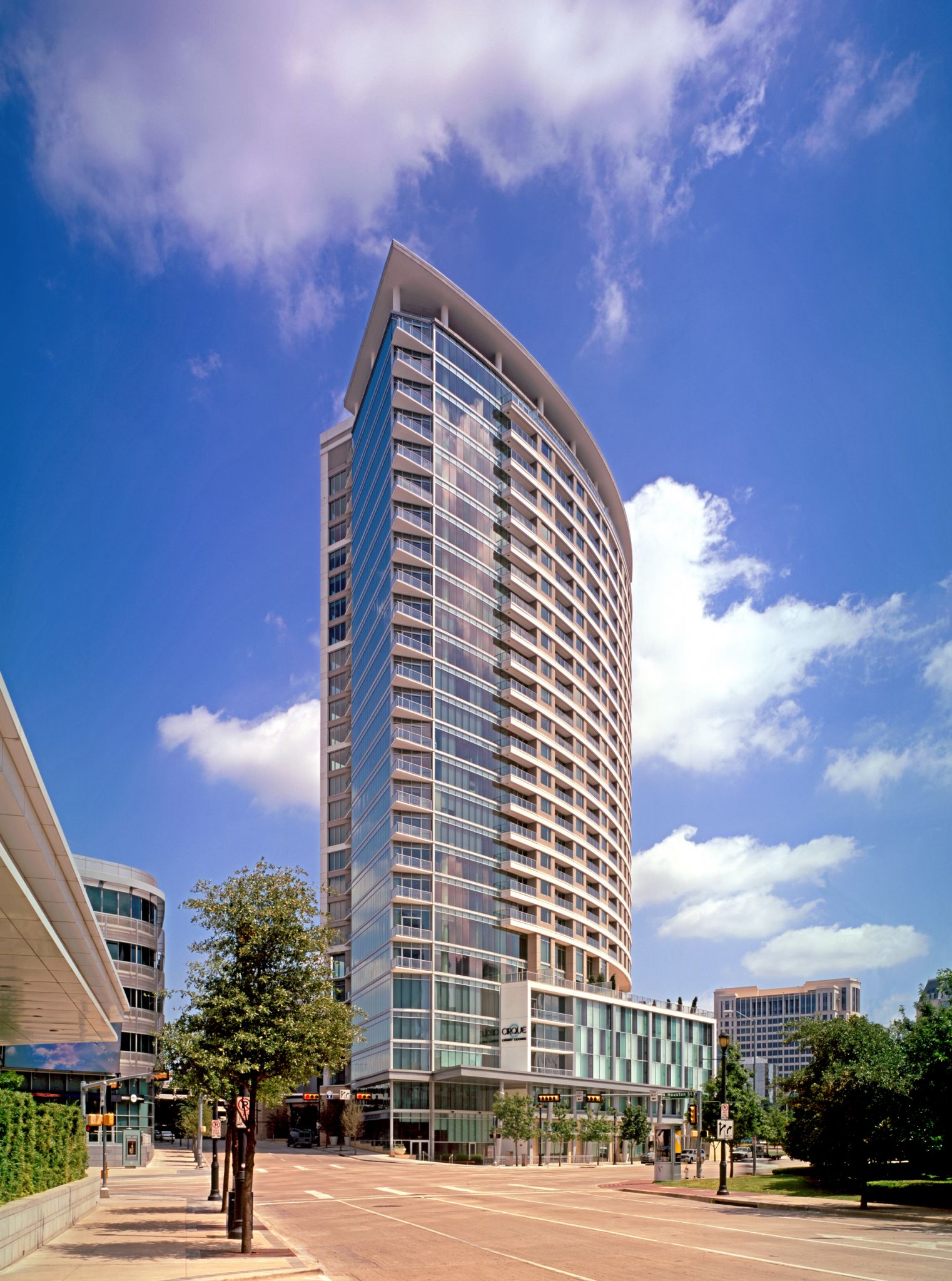
During the production of float glass, small nickel sulfide (NiS) inclusions can form due to minor contamination of the glass by nickel-bearing metal alloys (such as stainless steel). Minute nickel sulfide inclusions (or blemishes) found in the end result float glass are permitted under the ASTM C1036, Standard Specification for Flat Glass, depending on size and quality of the float glass.
Annealed or heat-strengthened glass may include nickel-sulfide inclusions that, due to the tempering process, may cause problems specific to a tempered glass product. Using controlled temperatures, the glass cooling procedure occurs at a much slower rate during the heat strengthening and annealing processes. This enables the presence of nickel-sulfide inclusions to complete a phase transformation and after expanding fully to their final size, remain stable following the cooling process.
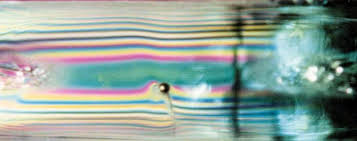
In the glass tempering process and during the rapid quench process, the nickel-sulfide particle-phase transformation is halted causing whatever nickel-sulfide inclusions that are present to be arrested in a compacted, pre-transformation state. Inclusions in this condition may be as small as 0.07mm to 0.38mm (0.003″ to 0.015″) in diameter. Particle inclusions of this size are invisible to the naked eye. When that tempered glass is later installed and exposed to varying temperatures of an outdoor environment, solar radiation, or other thermal stresses, nickel-sulfide inclusions can experience volumetric growth. If the particle expansion is large enough (typically around 4%), the stress caused by the NiS inclusions located in the center tension zone may cause the tempered glass to shatter.
In 2011, there were a series of highly publicized incidents involving spontaneous breakage of window glass that fell from high-rise buildings in Toronto, Chicago, Las Vegas, and Austin. Incidents of this type are rare, and they cannot be definitively attributed to NiS inclusions. However, the danger posed by spontaneous breakage has forced building code writers, architects and government officials to consider more widespread use of safety glass, where increased strength and risk reduction to bystanders are required.
HEAT SOAKING FLOAT GLASS
As previously mentioned, NiS inclusions are small, rare, and random, a combination that makes visual inspection for NiS inclusions nearly impossible. As an answer to that problem, and to reduce the risk of spontaneous glass breakage, many glass fabricators offer glass heat soaking as a solution.
During heat soaking, tempered float glass panels are loaded onto an A-frame cart, rolled into an oven and exposed to temperatures of 288°C to 316°C (550°F to 600°F). After the coldest glass panel reaches that temperature, a soak timer is started. The soak time is typically between two to eight hours. The objective of this heat soaking process is to fast track the phase change of any nickel-sulfide inclusion(s) present in the tension zone and to cause the float glass to break in the controlled environment of the oven rather than being shipped to a customer with the chance that it will spontaneously break after installation.
While this ‘break-it-now’ technique does catch defective tempered float glass panels by shattering them prior to shipment, it cannot guarantee 100% that spontaneous breakage won’t occur. An informal survey of glass manufacturers indicates that the probability of spontaneous breakage of tempered float glass that is not heat soaked is 9 out of every 1000 panels. With heat soaking, that number drops to 3 out of every 1000 panels.
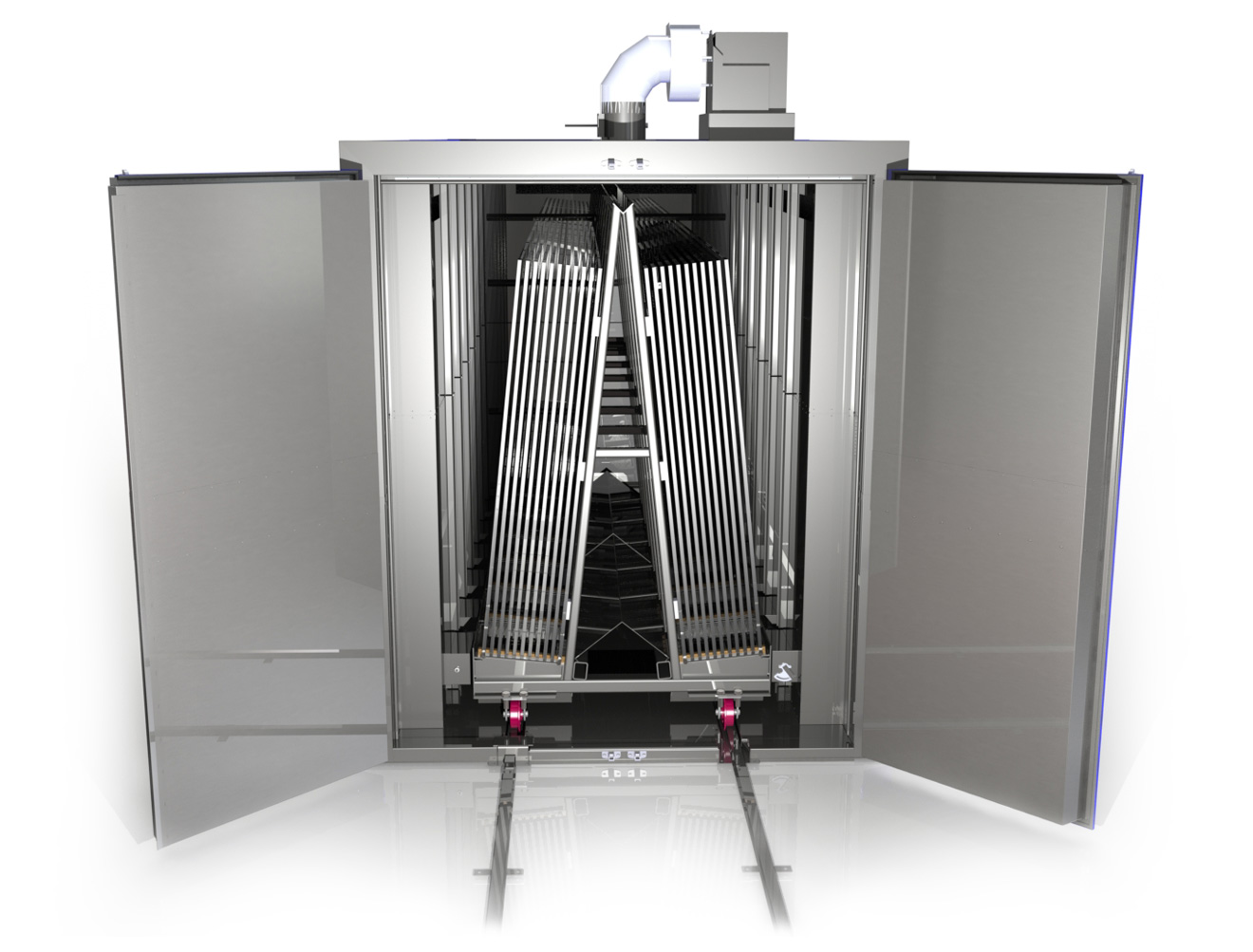
Heat soaking float glass provides a significant risk reduction, but it comes at a price. There is additional handling of the glass; personnel required to load and unload glass from the cart, the utility expenses of operating the heat soaking oven, increased reject rates due to scratches, edge damage or breakage, additional work-in-process inventory, shipping delays, etc.
Because it can be a significant cost, when presented with a proposal request for tempered glass, many glass manufacturers usually break-out the additional cost impact to heat soak the glass. It is then left to the architect and/or building owner to assess the risks against the increased price of the glass.
IMPROVEMENTS IN HEAT SOAKING OVENS
One of the challenges for today’s heat soaking ovens is to minimize the variance between the hottest and coldest part of the load. Remember, the entire load must be to the minimum threshold temperature prior to starting the soak timer.
Traditional heat soak ovens impinge air on the outside sheets of the A-frame cart and attempt to heat the inner sheets by blowing air below the cart in the hope that natural convection will allow the hot air to flow up between the glass panes.
One unique solution offered by Precision Quincy is to incorporate ductwork into the cart. This promotes substantial airflow between the glass panels, allowing faster heat-up and significantly improved temperature uniformity along the entire length and height of the glass. Faster heat-up means a shorter overall cycle time and more product throughput in a day. Changes in load density or thickness have little effect on the airflow and efficiency of this glass heat soak oven. See also our whitepaper page on Oven Cycle Dynamics.
CONCLUSION
Heat soaking is not a guaranteed practice to eliminate spontaneous breakage of tempered float glass. Yet, heat soaking float glass is the only proven method to test and contain glass panels that may be subject to contamination and possible failure due to nickel sulfide inclusions.
When selecting thermal processing equipment for heat soaking glass, it is important to work with a manufacturer with experience and expertise in this application to ensure proper airflow between the glass panels for efficient heat-up times and better temperature uniformity.