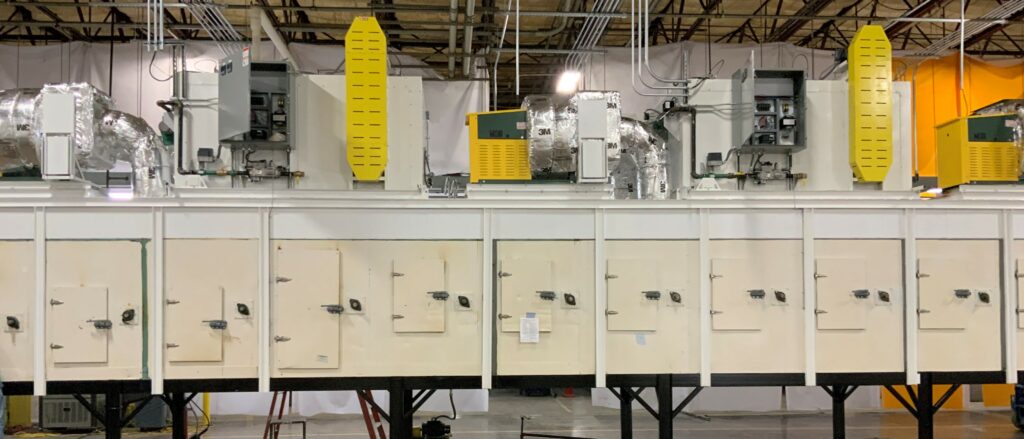
The decision on whether to retrofit or repair an industrial oven is always driven by a return-on-investment (ROI) analysis.
ROI = Benefit (or return) on investment / cost of the investment
To calculate ROI, both costs and benefits of the retrofit and repair project need to be quantified and compared to the alternative: whether it is purchasing new equipment or continuing to operate equipment as-is.
This guide contains a series of Questions and Answers intended to highlight factors that should be considered in formulating ROI. These insights have been derived from customer feedback and our experience working on these types of projects. It is our hope that these insights help to bridge the communication gap between accountants and engineers in our customer organizations when they are weighing the costs and benefits of a retrofit and repair project.
This guide should be read in conjunction with Nine Common Upgrades in Retrofit and Repair Projects for Custom Industrial Ovens. Quantifying the costs and benefits of a retrofit or repair project will depend on the nature of the upgrades.
Why are Retrofit Projects Less Expensive than Buying New Equipment?
Cost of Material
The major economic differentiation in a retrofit project (compared with buying new equipment) is the cost of material. In a retrofit project, our engineers will tailor a solution to replace only those components of the industrial oven that need to be replaced and will re-use other components.
For example, sometimes the oven shell does not need to be replaced (or replaced in full) because the oven operates at a low temperature (thus experiencing lower thermal stress) or because the original shell design and insulation was robust enough for the oven’s extended useful life.
Another example relates to the cost of conveyors and automation. Conveyors and automation can represent a significant portion of the total cost of material for new equipment; but in a retrofit project, these components can be reused and incorporated into the retrofit design.
Cost of Labor
The total cost of labor is also lower in a retrofit project because the scope of work is limited to those aspects of the oven that need to be repaired or redesigned. Labor rates can be higher for work that is performed in the field at the customer’s facility, but these additional costs are offset by the cost savings resulting from the tailored scope of the work and the significantly lower cost of material.
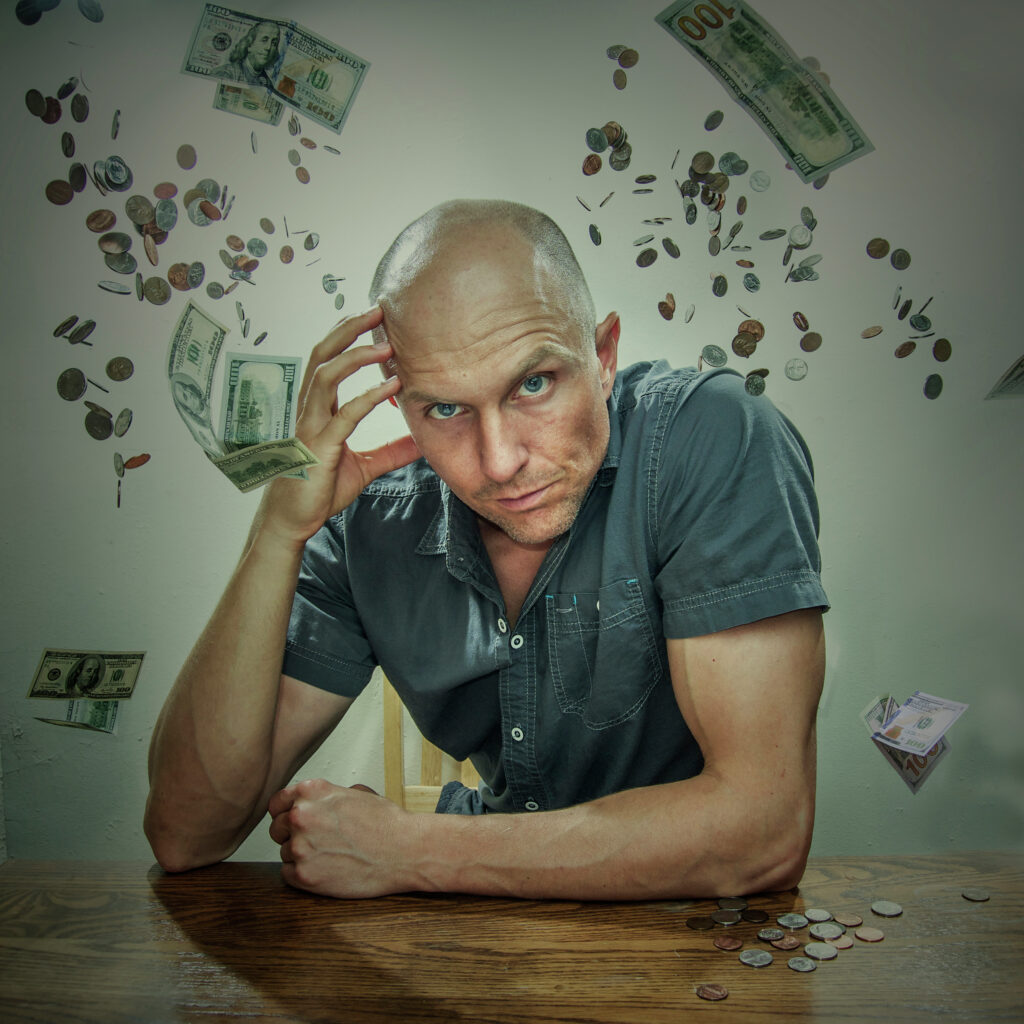
Can Any Industrial Oven be Retrofitted, or do the Economics Favor Only Certain Types of Industrial Ovens?
Any industrial oven can be repaired or retrofitted. These repairs vary in scope from replacing doors, heating elements and fans, to upgrading controls to integrate with reporting tools and other equipment. That said, retrofit projects make the most economic sense with larger or more customized industrial ovens. Consider these examples:
Monument-style Equipment
Many industrial ovens are fixed in place in a facility; and oftentimes, the building itself was constructed around the equipment. In these circumstances, the equipment removal costs, coupled with the cost of building modifications, significantly increase the ancillary costs associated with buying new industrial oven.
These costs can be reduced or eliminated in a custom engineered retrofit project which reuses significant portions of the existing oven.
Equipment with Conveyance or Automation
Many industrial ovens include custom-designed material handling systems and other automation to convey product based on its size, spacing, throughput and production rate. This equipment is often referred to as a conveyor (or sometimes a “continuous”) industrial oven.
These conveyors and automation often comprise a significant portion of a new industrial oven’s cost of material and can be reused and incorporated in the retrofit design.
Equipment Operated by Suppliers Requiring Customer Recertification
In some industries, suppliers are required to participate in a Production Part Approval Process (PPAP), which among other things, forces suppliers to certify capital equipment and production processes with the original manufacturer. PPAP, and other similar certification processes, are common in the automotive, aerospace and medical device industries.
Depending on the nature of the upgrades, these costly and time-consuming procedures may be avoided or become less burdensome in a retrofit project (compared with buying new equipment).
What is the Average Cost Savings for a Retrofit Project Compared to Buying New Equipment?
The cost of a retrofit or repair project can vary widely depending on the nature of the upgrades and type of oven. Remember that it does not make economic sense to retrofit every industrial oven. That said, for projects we have undertaken with customers, retrofits result in cost savings between 40% to 60%, compared with the cost of buying new equipment.
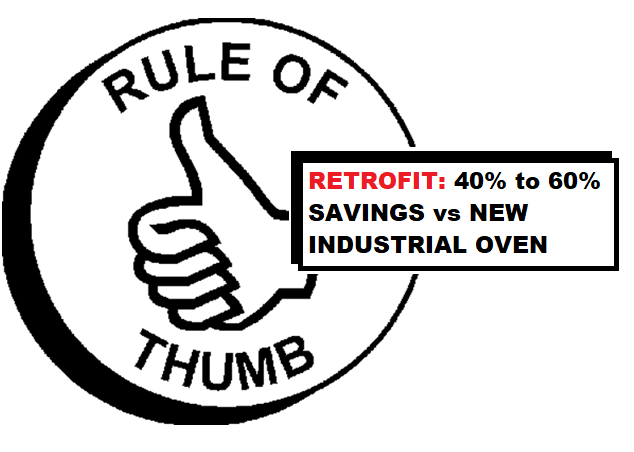
Does the Cost Savings in a Retrofit Project Depend on the Brand of Industrial Oven?
As mentioned above, the costs of a retrofit project can vary widely. That said, those variations in costs are not based on the brand of the original industrial oven.
All industrial ovens are bound by a common set of first order engineering principles, and any design must meet the standards promulgated by the National Fire Protection Association (NFPA). These principles and standards become the roadmap for any retrofit or repair project and do not vary based on the brand of the original manufacturer.
In What Circumstances do the Benefits Outweigh the Costs of a Retrofit Project?
Safety and Risk of Catastrophic Event
This one is important but sometimes overlooked by managers focused only on short term profit. The cost of a catastrophic event that damages a facility, other equipment or causes personal injury can be significant but the dollar amounts are difficult to project. That said, the risk of these costs should be an important consideration when evaluating a retrofit project.
Introduction of a New Product or Manufacturing Process
A retrofit project is often a good option when a new product or manufacturing process is introduced. Because retrofit projects involve a tailored approach to upgrades, the lead time for completing these projects is often faster than buying new equipment. As a result, production of the new product or with the new manufacturing process can commence sooner.
Quality and Throughput Issues Derived from Poor Original Design
It is a myth that custom equipment is always designed correctly the first time. In a retrofit project, feedback is solicited from the customer during the evaluation and concepting stages to address performance concerns. These performance issues can be expensive if they result in (a) poor quality resulting in expensive rejects or (b) slower throughput resulting in less volume.
In comparison, the design of new custom equipment does not benefit from the same iterative design process. Custom equipment by its nature is designed for the first and only time.
Are There Other Benefits of a Retrofit Project Compared to Buying New Equipment?
Shorter Lead Time and Less Downtime
As mentioned above, our engineers use a tailored approach to the design of a retrofit project. As a result, components of the oven are only replaced if necessary. When compared to buying new equipment, this tailored approach results in a faster engineering, manufacturing and installation process.
Conservation of Floorspace
New equipment usually needs to be installed in a different location at a customer’s facility, and the old oven is often not removed. This results in a less efficient use of floor space (with its associated cost) than in a retrofit project where the existing oven remains in place and is upgraded.
Reduced Disposal Costs
The cost of tearing down, removing and disposing of an old industrial oven is expensive. Although there can be disposal costs in a retrofit project, they are usually significantly less than if new equipment is purchased and old equipment is removed.
Are There Other Costs and Benefits of a Retrofit Project?
Reduced Energy Use
A major source of energy loss for a Class A batch oven is through the exhaust. The energy loss due to exhaust could be 50% of the total energy used in the oven. NFPA 86 (the standard governing industrial ovens) requires a fixed exhaust rate based on the amount of flammable material entering the oven per batch. This NFPA standard provides that even after the flammable material is no longer in the oven, the exhaust rate cannot be decreased.
In retrofit projects, we will investigate means to conserve energy attributable to exhaust. One way is to reduce processing time by improving energy transfer. We will also verify that the oven is not over-exhausting based on the amount of flammable material processed in the batch. In addition, we have installed LFL monitors which will reduce exhaust rates.
In addition to analyzing energy loss due to exhaust, we will also upgrade the oven shell (including insulation) and redesign the oven to improve air circulation by making changes to the combustion chamber and ductwork. These construction and design changes create opportunities for energy conservation (and a reduction in associated costs).
Reduced Maintenance Costs
Maintenance access is not a design priority for most manufacturers of industrial ovens. For this reason, many ovens are designed with minimal accessibility for the replacement of major components like fan wheels or shafts. In a retrofit project, we will make changes to the oven’s original design to improve ease of maintenance, which results in a reduction in the cost of that maintenance.