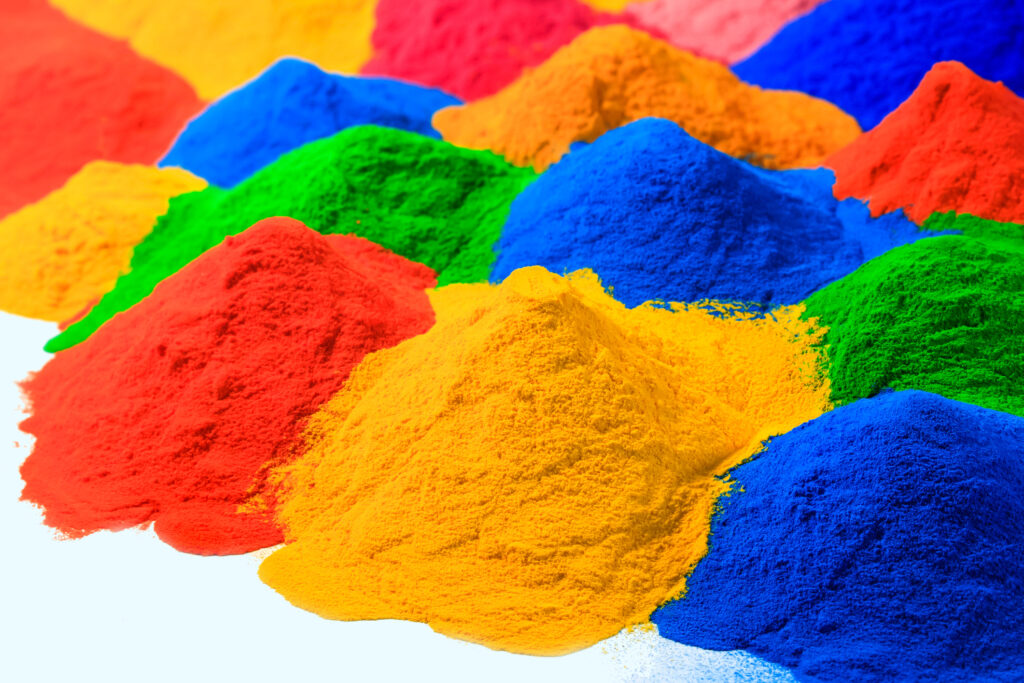
This guide provides an overview of the “basics” of powder coating for buyers of industrial ovens. It contains a series of questions and answers related to powder coating. Our objective in drafting this guide is to establish a foundation and common set of language that will facilitate further discussion with our customers and prospects.
What is Powder Coating?
Powder coating is a finishing process in which a dry powder made of polymer resins and other additives is applied to metal substrates and other materials such as plastics, composites, carbon fiber and medium-density fiberboard.
Unlike liquid paint, which is applied using an evaporating solvent, powder coating is applied using spray guns in a process called electrostatic spray deposition.
The coated product is then cured (or cross-linked) under heat to form a protective layer.
Once heat is applied, the materials crosslink to create a hard layer that is stronger than conventional paint.
Why Does Powder Coating Need an Industrial Oven?
After the part has been coated, it enters a curing oven where heat is transferred to the product by means of forced air convection or infrared heat.
When the powder heats up, the synthetic polymer chains bond with one another resulting in a coating layer with high cross-linked density.
This cure process is also called cross-linking, and it requires the correct combination of cure time and oven temperature.
What Material is Used in Powder Coating?
The polymer resins are made from epoxy, nylon, polyester or polyurethane, and can be either thermoplastic or thermoset in nature.
Thermoplastics can be reheated, remolded, and cooled as necessary without causing any chemical changes; whereas, thermosets are materials that strengthen when heated but cannot be remolded or heated after the initial forming.
Thermoplastic materials have a low melting point, and thermoset materials are better for higher temperatures.
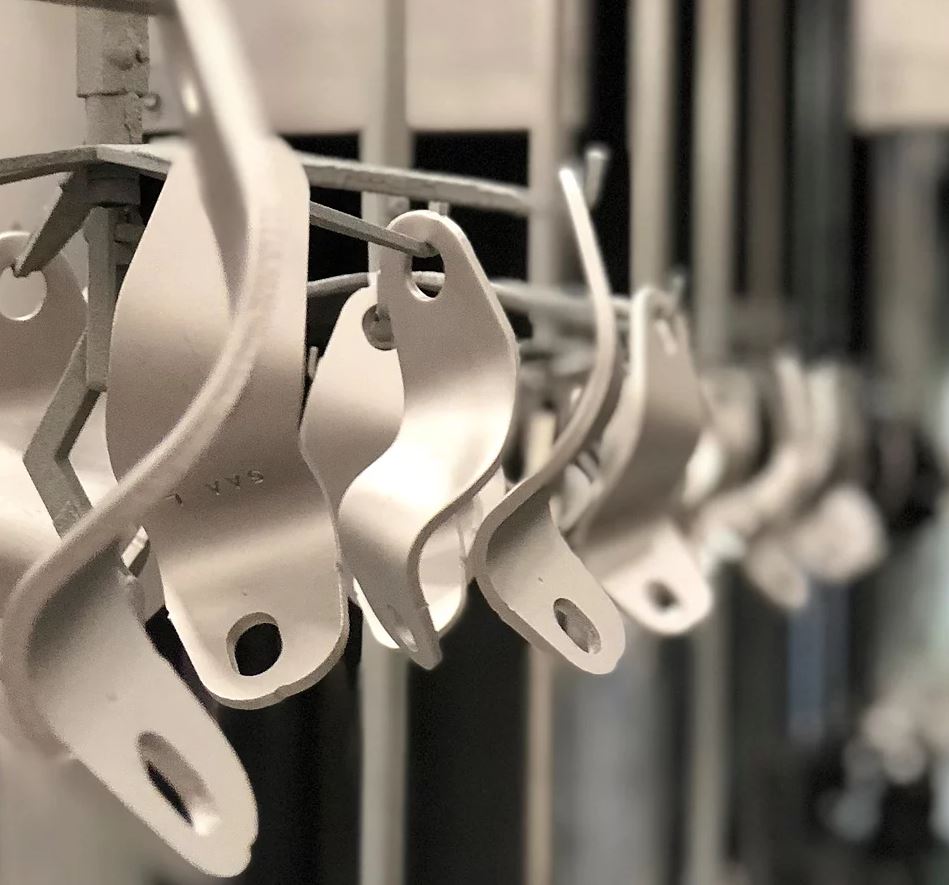
What Types of Ovens Can Be Used to Cure Powder Coating?
There are different types of powder coating ovens, including standard and custom ovens that range in different sizes: from small lab and cabinet batch ovens to large continuous systems. These ovens can be electrically heated or gas fired. Infrared or radiant-wall design is sometimes incorporated into the powder coating system for the preheating process.
Batch Ovens
Batch style ovens support a variety of applications and can accommodate products of various size, weight and shape. There are numerous ways that product can be loaded into a batch oven: from carts to ceiling mounted conveyor rails.
Continuous Ovens
Continuous ovens use conveyor systems to accommodate a closed loop system. These ovens typically use overhead monorail systems that move product through the different stages of the powder coating system: from load area, to powder paint booth, to cure oven and then to an unload area.
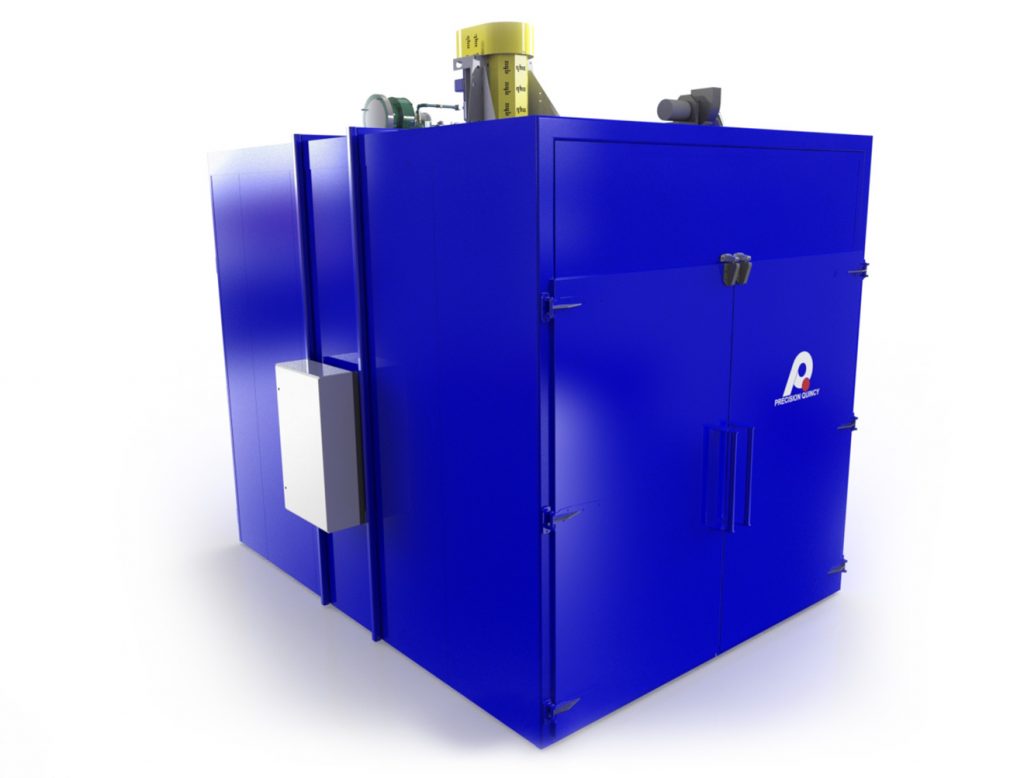
What Are the Benefits of a Powder Coating?
Powder coating is an economical and durable finishing that comes in almost any color. Powder coating surfaces do not fade and are resistant to rust, scratching, fading, chipping and other wear and tear.
Powder coating is also environmentally friendly because no solvent fumes are released and efficient because the electrostatic charge binds the powder coat to the metal or other material, preventing overspray.
Compared with wet paint, other benefits of powder coating include smoother texture, only one application is needed, longer lasting, safer and easier to store, eco-friendly and excess powder can be reused.
How Does a Powder Coating Oven Work?
Powder coating ovens are energy transfer units where energy is transferred to heat up parts in the oven through the medium of air. Industrial ovens contain enclosures which are constructed using insulated panels that contain the systems below.
Heater Unit
The heater generates and begins the distribution of energy to the parts in the oven. The heater unit includes the burner or other heating element, supply fan and filters.
Supply Air System
The purpose of the supply air system is to deliver and distribute the energy developed in the heater unit. This system also introduces fresh air from outside the oven. When fresh air is introduced, it lowers the temperature of the flame-heated air to reduce the production of NOx.
Recirculated Air System
The recirculating system returns oven air to the heater unit so that energy is continually added to the oven. This is accomplished using the duct with the supply fan to create a negative pressure condition within the enclosure. The oven air naturally migrates to the areas of low pressure, where it is captured in the duct system and returned to the heater.
Exhaust Air System
Every oven must be exhausted. Exhaust creates a negative environment so that air seals operate properly and remove cure products from the oven. In addition, the exhaust purges the oven prior to start-up.
What Applications Use Powder Coating?
Powder coating is used for coating metal substrates and other materials such as plastics, composites, carbon fiber and medium-density fiberboard. Powder coating is used in a variety of applications because it provides corrosion protection and outdoor durability.
Powder coating is commonly used in the industries listed below:
Agriculture | Furniture | Pharmaceuticals |
Aerospace | Heavy equipment | Pipe coating |
Appliances | Health industry | Plastics |
Architectural | Household furnishings | Steel fabrications |
Automotive | Lawn and garden | Recreational industry |
Coatings | Lighting | Restaurant equipment |
Cookware | Material handling | Sports equipment |
Entertainment industry | Military and defense | Telecommunications |
At What Temperature Does Powder Coating Cure?
The cure temperature depends on the type of powder coating used. The temperature range is commonly between 375 °F and 400 °F (190 – 204 °C).
How Long Does Powder Coat Take to Cure?
It depends on the temperature of the oven, the type of powder coating, and the characteristics of the material being cured. That said, a typical cure time is 30 to 40 minutes.
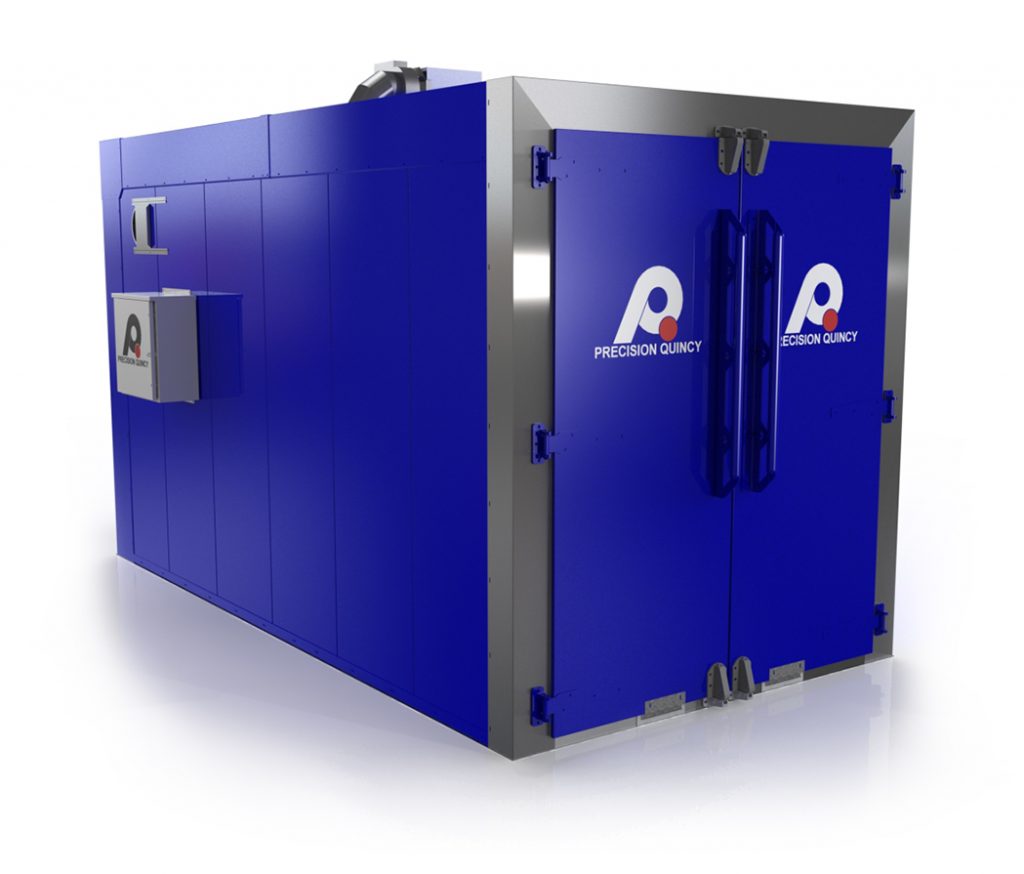
Do You Need an Industrial Oven to Cure Cerakote?
Cerakote is a trademarked name for a polymer-ceramic composite finishing that can be applied to wood, metal, plastics and polymers. Cerakote is used for its durability, scratch resistance, corrosion resistance, chemical resistance, impact strength, and hardness.
The process for curing Cerakote is similar to other powder coating processes, and an industrial oven is used in a similar way.
Usually, the oven temperature range is between 250 °F and 300 °F (121 – 149 °C) and the cure time is between one and two hours.
Does a Powder Coating Oven Need to Meet Any Industry Standards?
All powder coating ovens are required to meet the specification in NFPA (National Fire Protection Association) publication 86.
NFPA 86 is the roadmap for the design of all industrial ovens. It specifies the methods and devices required to meet industry standards.
Does Powder Coating Result in the Release of Volatile Organic Compounds (VOCs)?
Powder coating applications typically do not require solvents, and this process usually does not release VOCs into the atmosphere. As a result, thermal oxidizers or other pollution control equipment is usually not needed in order to comply with regulations from the US Environmental Protection Agency (EPA).
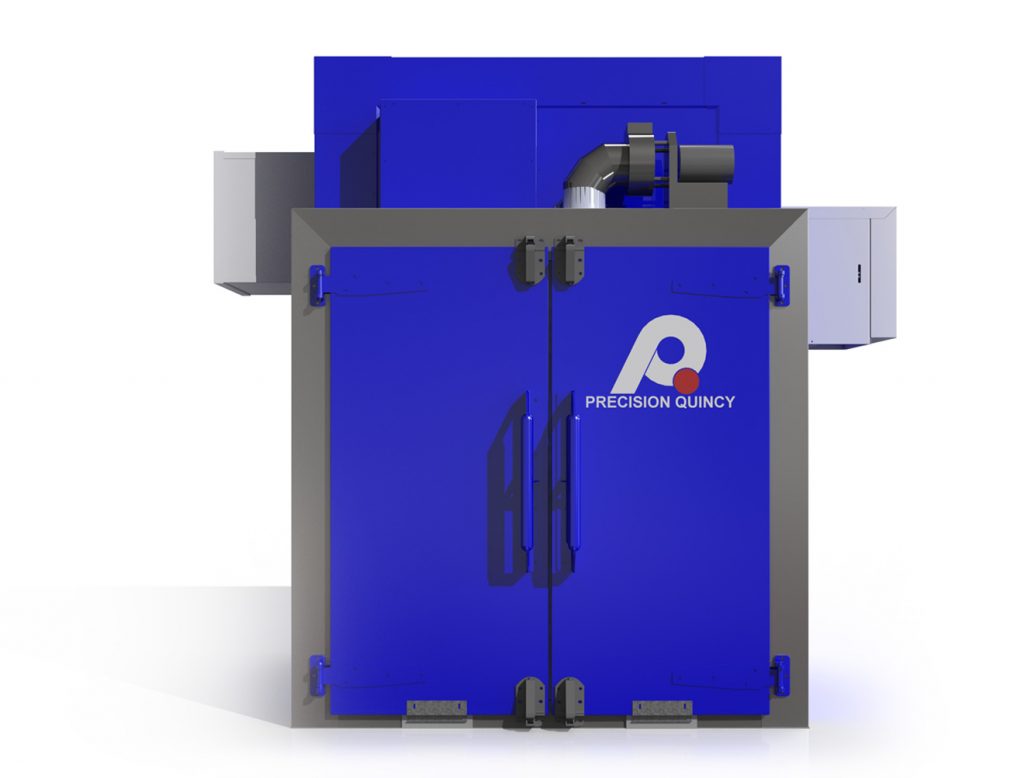
Is Powder Coating Toxic?
Most powder coating resins have little or no toxicity.
What is the Cost of Powder Coating?
Projecting the cost of powder coating depends on many variables. These variables include the type of powder coating, the size of the product, the volume of product, whether a batch or continuous closed-loop system is needed, whether the oven is electric or gas-fired, what kind of preparation is needed before coating (i.e., does the product need to be degreased, cleaned or sand blasted?).
How Often Do Powder Coating Ovens Need to be Maintained?
Proper monthly and annual maintenance and inspection schedules should be maintained.
Monthly maintenance should include an audit of the following:
- interior oven cleanliness,
- fuel safety shutoff valves,
- fan and air flow interlocks,
- time delay switch settings (purge),
- conveyor interlocks,
- limit switches,
- explosion relief latches,
- gas drip leg,
- high and low fuel pressure interlocks, and
- interior ductwork cleanliness.
Annual maintenance and inspection should include:
- operating sequence tests,
- calibration of instruments,
- flame failure system components,
- checking burner and ignitors,
- wiring and piping,
- inspection of the combustion air supply system and combustion control system, and
- automatic fire checks.
Can Powder Coating Ovens be Rebuilt, Retrofitted or Moved?
Any industrial oven can be repaired or retrofitted. These repairs vary in scope from replacing doors, heating elements and fans, to upgrading controls to integrate with reporting tools and other equipment.
For powder coating ovens, rebuilds and retrofits make the most sense when the oven is fixed in place in a facility (so-called “monument-style” equipment) or when the equipment is designed with conveyors or other material handling systems that can be reused or incorporated into the retrofit design.
Powder coating ovens can be moved, but we recommend working with professionals that understand industrial oven technology. See Retrofits.